Sản xuất dung dịch H2SO4 được công nghiệp hóa từ lâu bởi nhu cầu sử dụng loại hóa chất này trong đời sống cũng như trong sản xuất là rất lớn. Tuy nhiên một số công nghệ cũ chưa được hoàn thiện cần được cải tiến để đạt hiệu quả cao nhất cũng như giảm ảnh hưởng tới môi trường.
1 Giảm lãng phí năng lượng.
Trong sản xuất H2SO4 theo phương pháp đốt lưu huỳnh, khoảng 98% năng lượng đưa vào là năng lượng hóa học tự có của các chất tham gia phản ứng. Phần nhiệt còn lại được đưa vào qua hệ thống quạt, dưới dạng năng lượng nén. Thông thường, khoảng 57,5% tổng năng lượng được thu hồi ở dạng hơi cao áp, khoảng 3% mất đi cùng khí đuôi qua ống khói, 0,5% mất đi ở dạng nhiệt lượng của axit thành phẩm, 39% bị mất đi ở dạng nhiệt thải trong hệ thống làm lạnh axit. Các tỷ lệ nói trên có thể thay đổi theo hàm lượng SO2 trong khí đầu ra của lò đốt lưu huỳnh, nhưng nói chung chúng có xu hướng được giữ nguyên.
Vấn đề ở đây là hơn 1/3 năng lượng tích lũy ở dạng nhiệt thải bị hoang phí. Hiện nay, việc cải tiến công nghệ giúp thu hồi và sử dụng lượng nhiệt năng này cho một số mục đích khác như:
– sản xuất nước nóng để cô đặc H2SO4 trong nhà máy
– sản xuất nước nóng cung cấp cho các cơ sở sản xuất liền kề
– sản xuất nước nóng cho hệ thống cung cấp nước nóng sinh hoạt ở địa phương
Tuy nhiên, vấn đề là phải tìm ra những vật liệu thích hợp để chế tạo các thiết bị trao đổi nhiệt có hiệu quả cao và có khả năng vận hành lâu dài trong môi trường ăn mòn mạnh. Ở mặt tiếp xúc, các vật liệu này phải chịu được cả axit sunphuric ở 160 – 190 oC có nồng độ 94 – 99%, và chịu được áp suất của nước nồi hơi đến 0,5-1 MPa. Vấn đề giá thành của các vật liệu này cũng là yếu tố quan trọng ảnh hưởng đến quá trình sản xuất H2SO4.
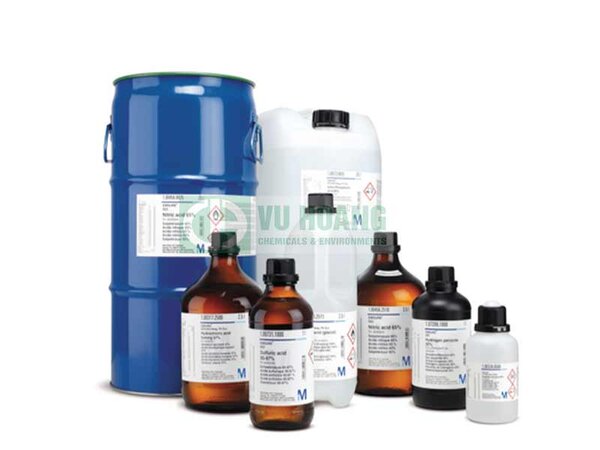
2 Cải tiến các công đoạn hấp thụ và làm lạnh
Khi nhiệt độ tăng, các tháp hấp thụ thông thường trong dây chuyền sản xuất axit sunphuric sẽ đạt đến giới hạn hoạt động của chúng. Để có thể sử dụng axit nhiệt độ cao mà không làm giảm hiệu suất hấp thụ thì cần phải cải tiến, nâng cao hiệu quả cả hai công đoạn làm lạnh và hấp thụ bằng cách sử dụng các tháp venturi.
Một bên tháp, khí chứa SO3 đi vào với nhiệt độ khoảng 300oC, đầu kia của tháp là axit có nhiệt độ khoảng 170oC. Do hấp thụ và phản ứng với SO3 nên nhiệt độ axit tăng lên đến 195oC. Khoảng 95% SO3 chứa trong khí được hấp thụ ở phần venturi, nồng độ H2SO4 được quan sát và kiểm tra trong hệ tuần hoàn của tháp venturi.
Axit nóng chảy xuống dưới được bơm qua lò hơi để trao đổi nhiệt rồi lại được đưa về tháp venturi. Lò hơi sản xuất hơi bão hoà 0,5 MPa, hơi này có thể được sử dụng trực tiếp trong nhà máy. Hệ thống làm lạnh axit được thiết kế sao cho có thể lấy đi được 60% nhiệt hấp thụ ban đầu trong trường hợp hệ thống thu hồi năng lượng gặp trục trặc.

Bộ phận sản xuất hơi nước là một thiết bị bốc hơi kiểu lò hơi đặc biệt, được nối bằng mặt bích với một thiết bị trao đổi nhiệt kiểu ống chùm. Axit sunphuric nóng được làm lạnh rồi phun vào đỉnh tháp venturi qua nhiều vòi phun. Nồng độ axit được khống chế bằng cách bổ sung nước vào bộ phận thu gom axit của tháp venturi. axit nóng dư, tạo ra trong hệ tuần hoàn của tháp venturi, sẽ chảy vào thùng chứa, sau đó được sử dụng để gia nhiệt sơ bộ nước nạp nồi hơi. Với nước cấp cho nồi hơi ở 105oC và hệ hấp thụ kép có các dòng chảy tuần hoàn, có thể thu hồi đến 0,5 tấn hơi nước áp suất thấp trên mỗi tấn axit. Hơi nước cao áp và thấp áp có thể được nạp phối hợp vào tuabin phát điện. Công suất điện thu được đạt xấp xỉ 430 kW/tấn H2SO4.
Đây là một cách không chỉ tận dụng được nguồn năng lượng mà còn giảm hiệu ứng nhà kính, góp phần lớn cho vấn đề bảo vệ môi trường
3 Cải tiến các hệ thống an toàn
An toàn sản xuất là vấn đề quan trọng của tất cả các nhà máy. Với nhà máy sử dụng các thiết bị, hóa chất độc hại càng phải yêu cầu cao về vấn đề bảo đảm an toàn. Ngoài trang bị các thiết bị, đồ bảo hộ lao động cho công nhân, Một số thiết bị cần được bổ sung so với các hệ thống cũ như:
– hệ thống đo liên tục tốc độ ăn mòn.
– hệ thống quan sát rò rỉ, có còi hoặc đèn báo hiệu.
– hệ thống đo độ dẫn điện, dẫn nhiệt, độ pH của nước nồi hơi, kết hợp với hệ thống khóa liên động tương ứng.
Không có nhận xét nào:
Đăng nhận xét